Innovation in electronic metal melting
Flawless castings for every sector
Since 1948 we design and manufacture electronic casting machines, The aim of this project is to develop a new type of electronic melting facility for special metals and precious alloys for goldsmiths, dentists and industrialists.
Pioneers in electronic fusion
Galloni ASEG was the first company in the world to realize induction electronic melting, continuing to develop innovative technological solutions for metal melting processes.
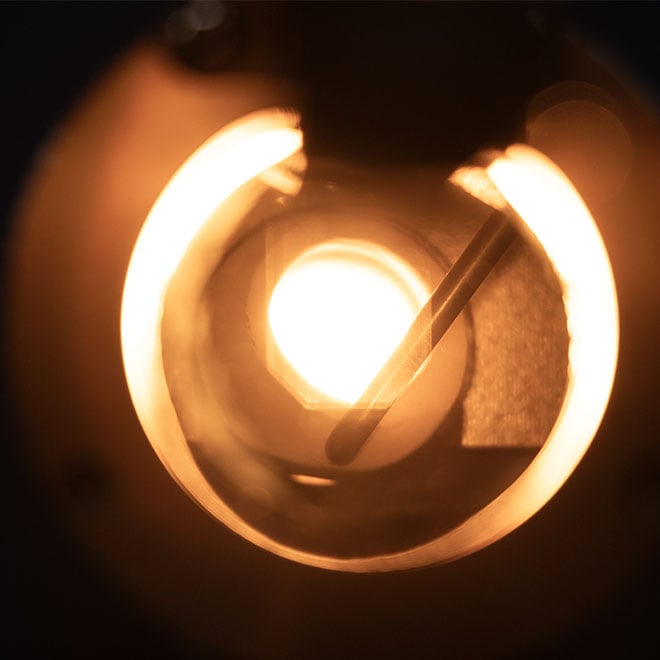
Precious metal casting courses
In our Teaching Centre we share our experience and expertise, offering our customers high-level training for precious metals casting.
The secrets of casting
Learn more about fusion with our exclusive casting guide. A practical and detailed manual, available for download, to guide you step by step in the process of metal casting.
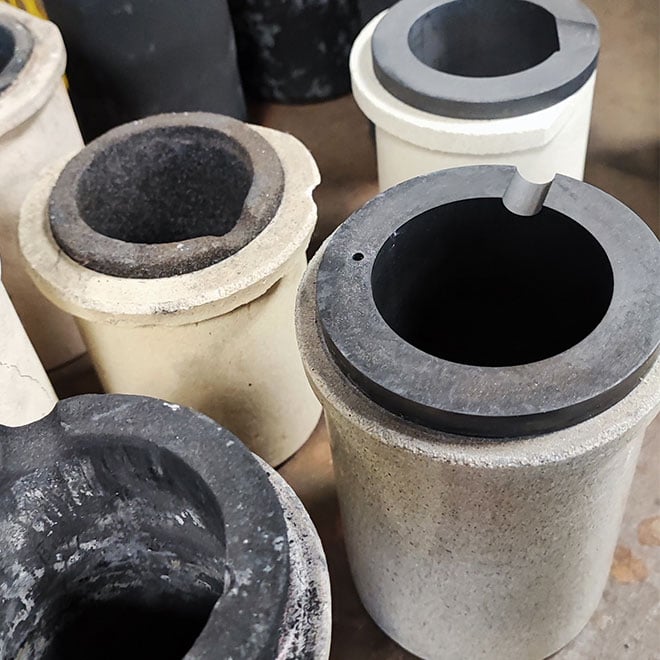
Dealers Galloni ASEG: our global network
Find your nearest ASEG Galloni partner. With a network of dealers around the world, we are always on hand to provide you with support, advice and access to our innovative products wherever you are.
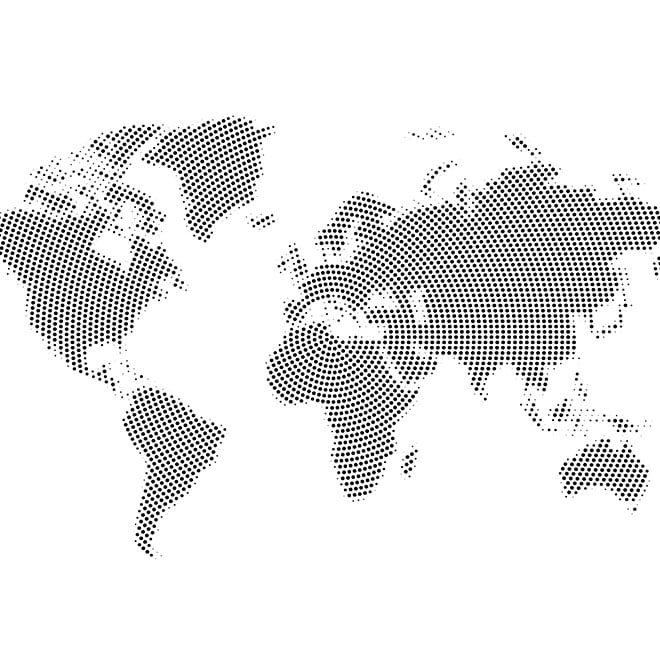
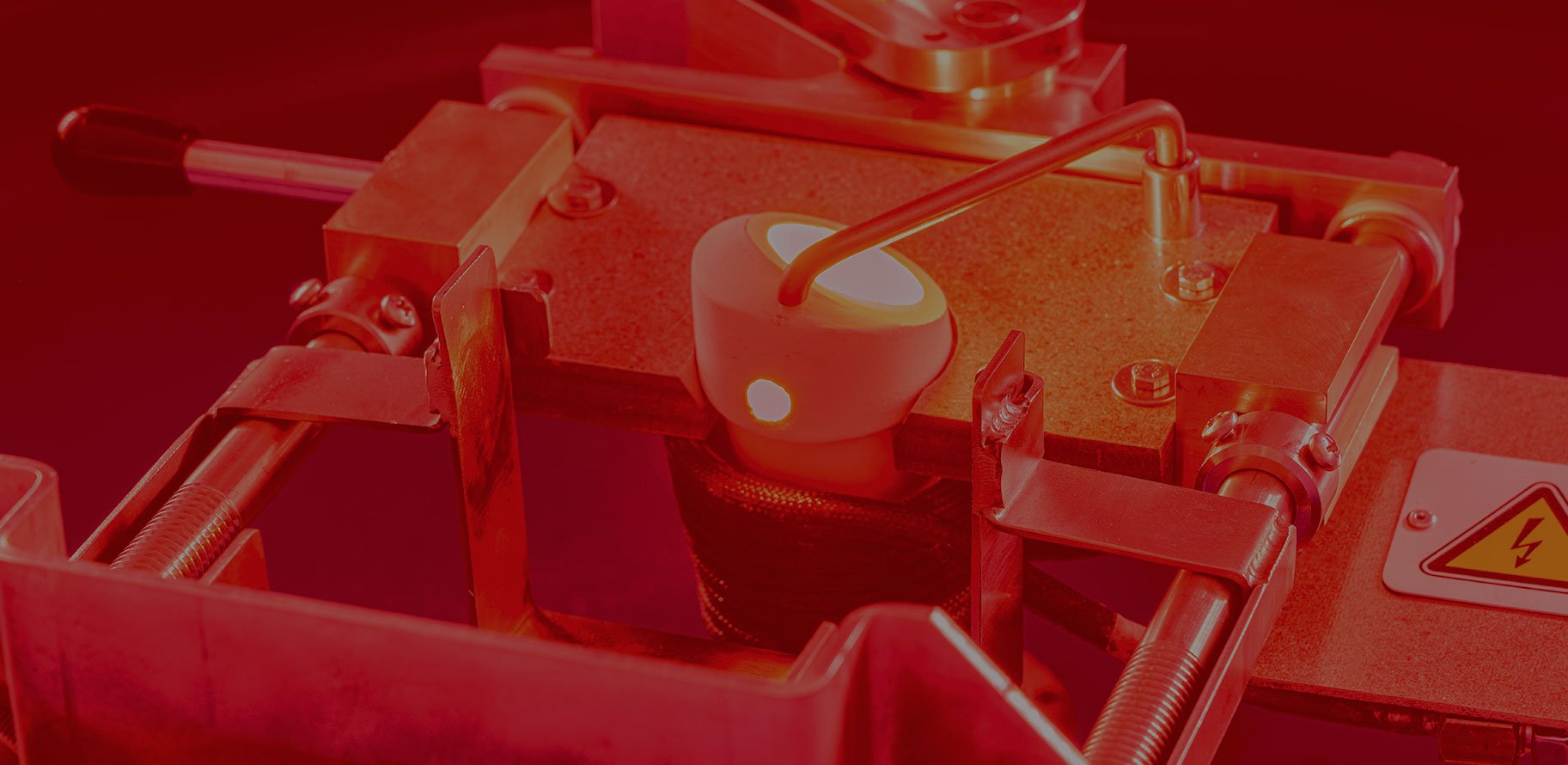
Contact us for information
Are you ready to take your casting quality to a new level? Contact us today to find out how our innovative solutions can transform your work.